Magnetic robots walk, crawl, and swim
New soft-bodied robots that can be controlled by a simple magnetic field are well suited to work in confined spaces.
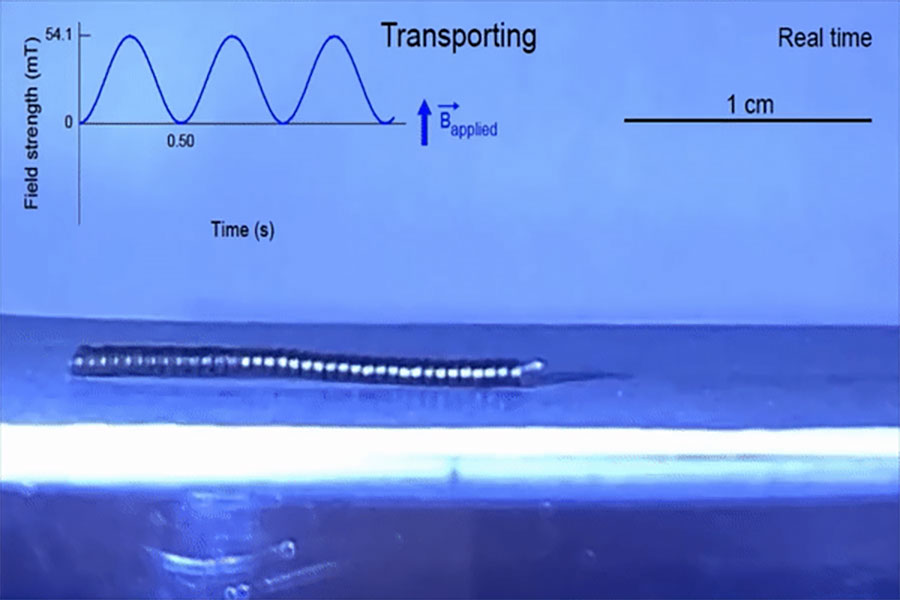
MIT scientists have developed tiny, soft-bodied robots that can be controlled with a weak magnet. The robots, formed from rubbery magnetic spirals, can be programmed to walk, crawl, swim—all in response to a simple, easy-to-apply magnetic field.
“This is the first time this has been done, to be able to control three-dimensional locomotion of robots with a one-dimensional magnetic field,” says McGovern associate investigator Polina Anikeeva, whose team reported on the magnetic robots June 3, 2023, in the journal Advanced Materials. “And because they are predominantly composed of polymer and polymers are soft, you don’t need a very large magnetic field to activate them. It’s actually a really tiny magnetic field that drives these robots,” says Anikeeva, who is also the Matoula S. Salapatas Professor in Materials Science and Engineering and a professor of brain and cognitive sciences at MIT, as well as the associate director of MIT’s Research Laboratory of Electronics and director of MIT’s K. Lisa Yang Brain-Body Center.
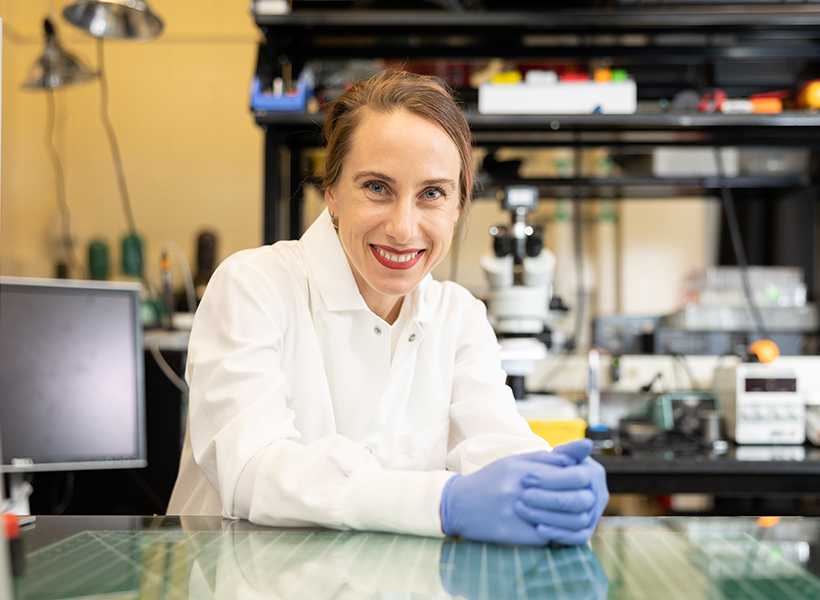
The new robots are well suited to transport cargo through confined spaces and their rubber bodies are gentle on fragile environments, opening the possibility that the technology could be developed for biomedical applications. Anikeeva and her team have made their robots millimeters long, but she says the same approach could be used to produce much smaller robots.
Engineering magnetic robots
Anikeeva says that until now, magnetic robots have moved in response to moving magnetic fields. She explains that for these models, “if you want your robot to walk, your magnet walks with it. If you want it to rotate, you rotate your magnet.” That limits the settings in which such robots might be deployed. “If you are trying to operate in a really constrained environment, a moving magnet may not be the safest solution. You want to be able to have a stationary instrument that just applies magnetic field to the whole sample,” she explains.
Youngbin Lee, a former graduate student in Anikeeva’s lab, engineered a solution to this problem. The robots he developed in Anikeeva’s lab are not uniformly magnetized. Instead, they are strategically magnetized in different zones and directions so a single magnetic field can enable a movement-driving profile of magnetic forces.
Before they are magnetized, however, the flexible, lightweight bodies of the robots must be fabricated. Lee starts this process with two kinds of rubber, each with a different stiffness. These are sandwiched together, then heated and stretched into a long, thin fiber. Because of the two materials’ different properties, one of the rubbers retains its elasticity through this stretching process, but the other deforms and cannot return to its original size. So when the strain is released, one layer of the fiber contracts, tugging on the other side and pulling the whole thing into a tight coil. Anikeeva says the helical fiber is modeled after the twisty tendrils of a cucumber plant, which spiral when one layer of cells loses water and contracts faster than a second layer.
A third material—one whose particles have the potential to become magnetic—is incorporated in a channel that runs through the rubbery fiber. So once the spiral has been made, a magnetization pattern that enables a particular type of movement can be introduced.
“Youngbin thought very carefully about how to magnetize our robots to make them able to move just as he programmed them to move,” Anikeeva says. “He made calculations to determine how to establish such a profile of forces on it when we apply a magnetic field that it will actually start walking or crawling.”
To form a caterpillar-like crawling robot, for example, the helical fiber is shaped into gentle undulations, and then the body, head, and tail are magnetized so that a magnetic field applied perpendicular to the robot’s plane of motion will cause the body to compress. When the field is reduced to zero, the compression is released, and the crawling robot stretches. Together, these movements propel the robot forward. Another robot in which two foot-like helical fibers are connected with a joint is magnetized in a pattern that enables a movement more like walking.
Biomedical potential
This precise magnetization process generates a program for each robot and ensures that that once the robots are made, they are simple to control. A weak magnetic field activates each robot’s program and drives its particular type of movement. A single magnetic field can even send multiple robots moving in opposite directions, if they have been programmed to do so. The team found that one minor manipulation of the magnetic field has a useful effect: With the flip of a switch to reverse the field, a cargo-carrying robot can be made to gently shake and release its payload.
Anikeeva says she can imagine these soft-bodied robots—whose straightforward production will be easy to scale up—delivering materials through narrow pipes or even inside the human body. For example, they might carry a drug through narrow blood vessels, releasing it exactly where it is needed. She says the magnetically-actuated devices have biomedical potential beyond robots as well, and might one day be incorporated into artificial muscles or materials that support tissue regeneration.